Maintenance, repairs, and equipment issues aren’t the most comfortable topics in any industry, including solar. Manufacturers, installers, and customers often overlook or avoid conversations. Despite the awkwardness of the conversation, it’s worth having to set expectations at the beginning.
Rather than avoiding the conversion, let’s explore solar energy system maintenance required by a solar energy system, the equipment most likely to necessitate maintenance or repair, the associated costs, and strategies to mitigate negative consequences.
Table of Contents
How Much Maintenance Will a Solar Energy System Need?
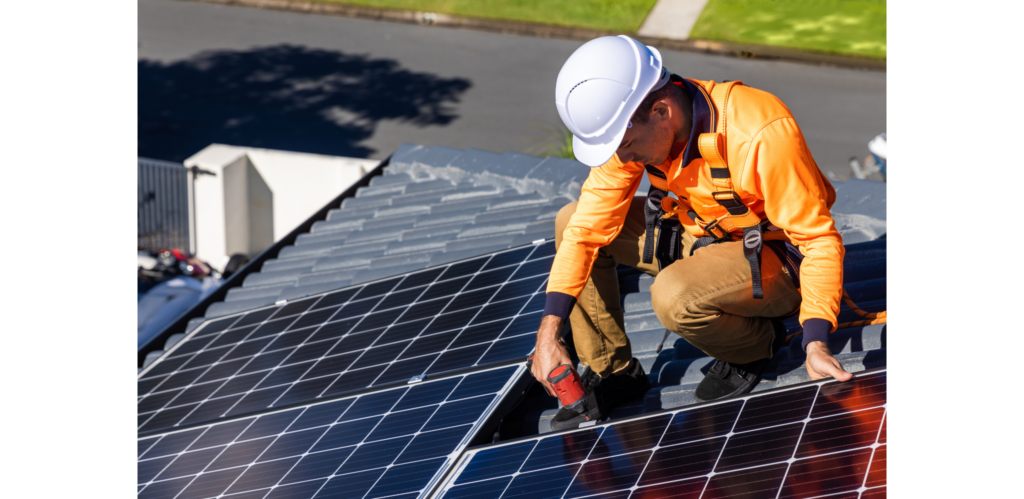
While it’s become common among solar sales reps to describe systems as “set it and forget it” or “there’s no moving parts,” the reality is that solar energy systems will require maintenance during their lifetime. Any piece of equipment with a normal lifespan of 25+ years isn’t going to run completely maintenance-free forever.
Typical equipment warranties:
- 12-25 years on Inverters
- 25 years on Panels
- 10-15 years for Batteries
So if any of the equipment fails, its replacement will likely be covered under a warranty, allowing homeowners to get a new product at no additional cost. However, in most cases, homeowners will usually have to pay for labor for someone to come out and install the replacement. According to HomeAdvisor, labor to swap out a piece of equipment can vary and cost upwards of $75-250 per hour.
But “maintenance” isn’t just defined as equipment failure. Maintenance can be anything that requires work done by either the owner or installer. Sometimes problems are simple connectivity issues that only require turning the inverter off and back on again. Other times, maintenance requires someone on-site to diagnose and repair an issue.
If you live in a dry arid region or near a coast, panels may also need to be cleaned to keep them in peak operating conditions. It’s good practice for solar homeowners and solar installers to check in at least once a year just to ensure there are no flagrant issues. Solar homeowners should also regularly check their monitoring portal so they know how much their system is producing and if any errors are present.
The Most Common Causes
There are many causes of maintenance in solar energy systems, but the ones that lead to the most labor costs are, by far and away, equipment failures. Solar energy systems have three major pieces of equipment that could fail: panels, inverters, and batteries. Batteries have only started to reach mass adoption in the past few years, so not much practical failure rate data is available. But when it comes to panels vs inverters, inverters have a significantly higher failure rate.
Inverters failing more often than panels makes a lot of sense. Panels, while being the most recognizable part, are relatively simple. Panels are made up of a few layers squished together and produce energy through a physical and chemical phenomenon called the photovoltaic effect. The generated electricity flows through wires, and that ends the panel’s involvement. According to a 2017 study by the National Renewable Energy Lab (NREL) found that panel installations between 2000 and 2015 exhibited a median failure rate of 5 out of every 10,000 panels.
Inverters, on the other hand, have the much more intensive job of converting DC energy into AC energy, regulating voltage and frequency, interacting with a home and the grid, and monitoring a system. Because they handle a much heavier load and have more parts, they are more likely to experience issues.
The failure rate of inverters also differs by the type of technology being utilized. We previously published a research study that looked at claims data from 100,000 solar energy systems across 5 years.
Our research found that string inverters experience a failure rate in the first two years of operation of approximately 0.89%, meaning roughly 89 out of every 10,000 units would fail during their first two years of operation. Microinverters, on the other hand, experienced a failure rate of 0.0551%, or roughly 5.5 out of every 10,000 units.
Both technologies’ failure rate has also improved substantially since 2017.
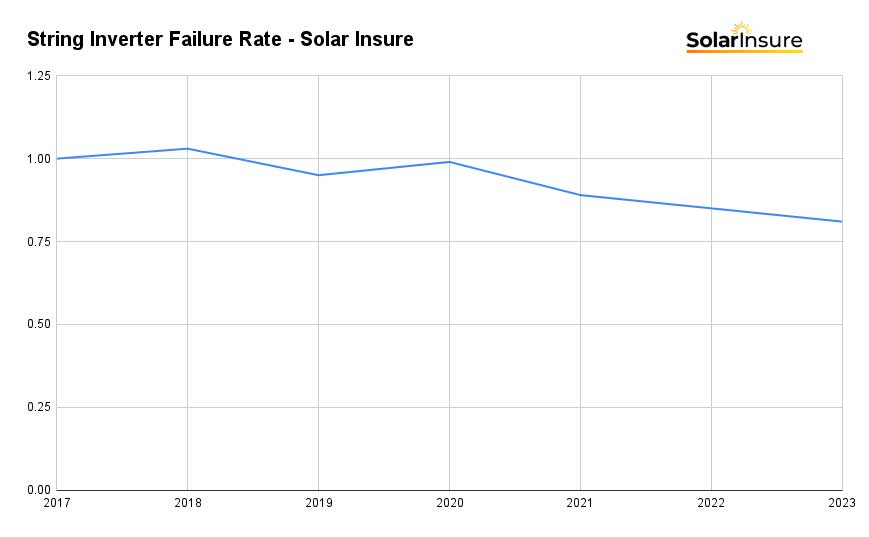
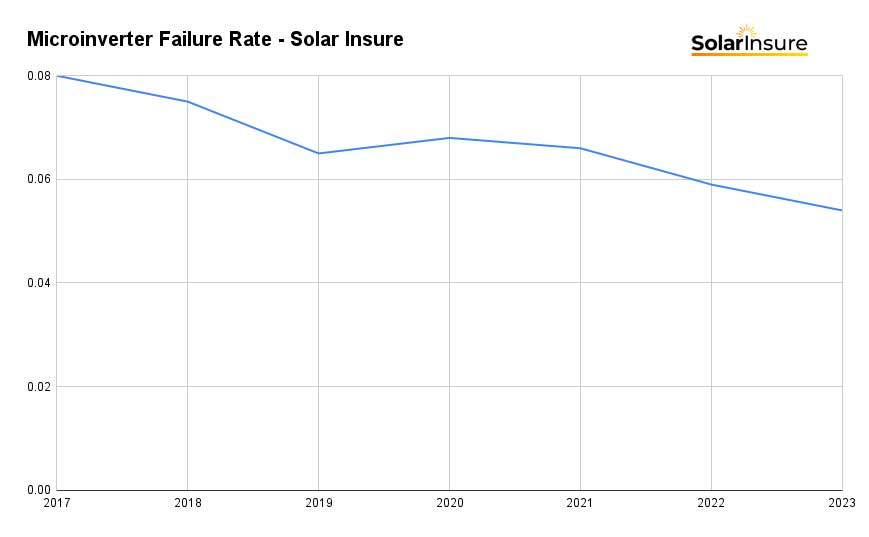
Maintenance Costs
While failure rates in early operation differ by a fair margin, are were some interesting data points on failure time and cost. Our research found that microinverters’ average failure time was at 261 days post-installation, while string inverters had a slightly longer failure time of 269 days post-installation. This would suggest that while microinverters failed less frequently, those that did fail did so sooner.
Microinverters were more costly to repair than string inverters. Our research found that a microinverter replacement claim payout averaged $464, while string inverter replacement claims averaged $432. This makes sense: when replacing microinverters, it involves climbing on a roof and removing one or several panels to access the faulty piece of equipment. String inverters, on the other hand, are often mounted at ground level and only have one component to replace.
So, how much does solar maintenance cost? Well, that answer depends on the solar installer performing the service. Many organizations will charge a few hundred dollars just to send a technician out to the site, then a flat rate per hour to perform maintenance. Depending on what needs to be done, a technician could be on site for 1-2 hours or or an upwards of 4-8 hours.
Unless protected by an independent warranty, installer warranty, or extended service agreement, solar homeowners should expect to pay several hundred dollars for the replacement of a failed component.
How to Mitigate Solar Maintenance Costs
There are a few different ways to mitigate service costs in solar. First and foremost is active monitoring. Homeowners and solar installers should regularly check online monitoring platforms to ensure proper operation. Issues can often be resolved remotely through power cycling or firmware updates to get systems back up and running. However, the failed equipment can’t be replaced remotely.
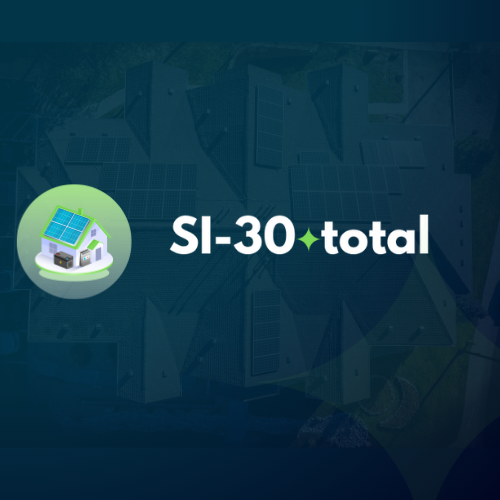
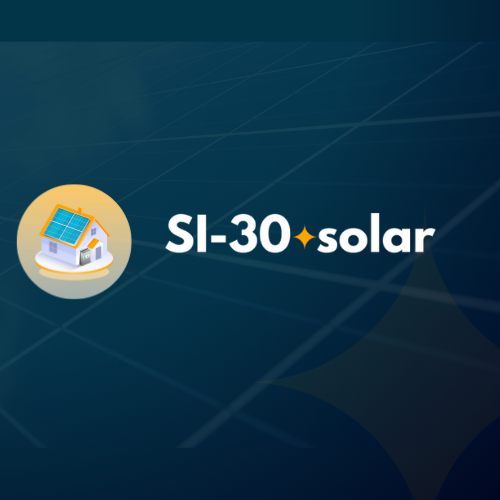
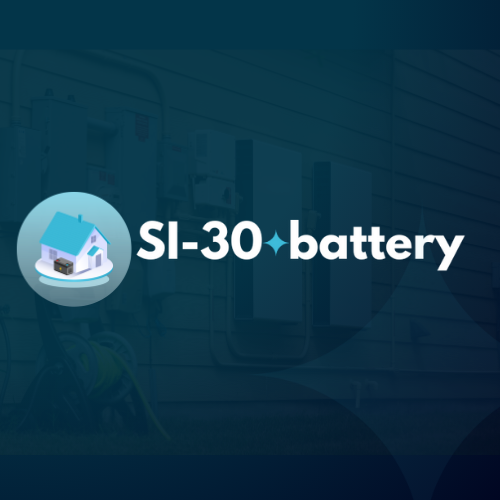
For newly installed systems, the best way to mitigate service costs is with SI-30 warranties from Solar Insure. With SI-30 Total, SI-30 Solar, and SI-30 Battery, solar installers provide homeowners protection and peace of mind with 30 years of equipment and labor cost coverage. Installers can perform service work as necessary and submit claims to Solar Insure to be paid for their service work, so costs don’t need to be passed on to consumers. The SI-30 products also carry Manufacturer Default Protection, so if a manufacturer becomes insolvent, homeowners don’t need to worry about losing out on their warranty.
If you’re a homeowner with solar already but your solar installer went out of business or you don’t have a reliable maintenance provider, you have a great option in SolarDetect.
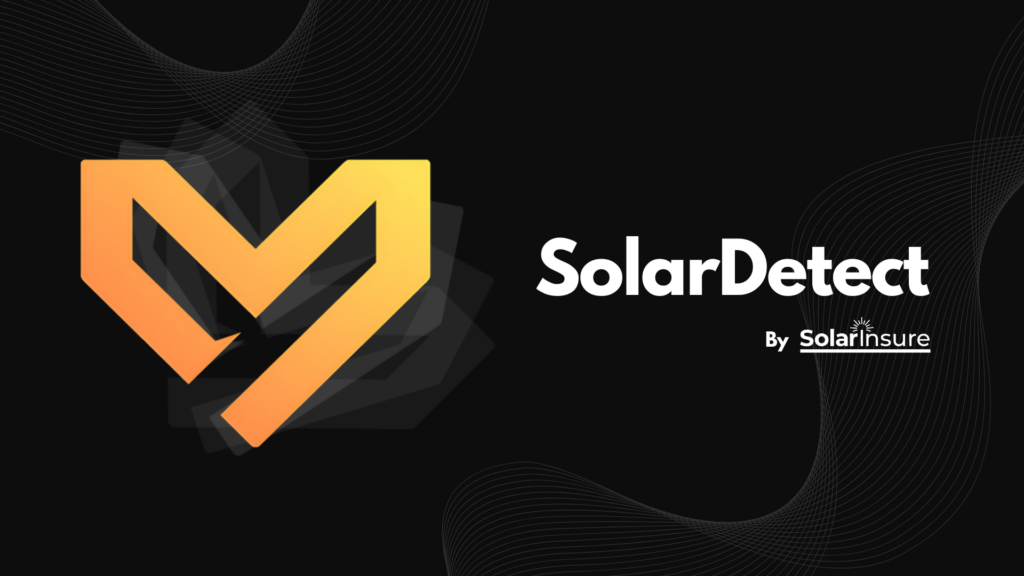
SolarDetect is a solar system maintenance solution for homeowners. SolarDetect provides coverage for critical system components like panels and inverters, and labor cost coverage. Our team of experts checks your solar energy system and attempts to remotely troubleshoot issues when a claim is made or if issues are found during monthly reporting. But if solar panel maintenance or solar inverter repair are needed, we’ve got a network of local, certified service providers whom we work with to get your system back up and running. SolarDetect handles all the hassle of working with manufacturers and repair teams, so homeowners can sit back and enjoy truly worry-free energy and peace of mind.
SolarDetect is backed by Zurich North America to bring an additional safety net to homeowners.
Visit detect.solarinsure.com to see if you’re eligible for SolarDetect, or speak to your solar installer about SI-30 warranties if you’re just getting started on your solar journey.